Linie montażowe są wszędzie tam, gdzie występuje produkcja masowa. Od telefonów komórkowych, przez samochody, aż po samoloty — prawie wszystkie produkty wytwarzane w dużych ilościach powstają na liniach montażowych. Rozejrzyj się wokół siebie i spróbuj znaleźć coś, co NIE zostało wyprodukowane na linii montażowej. Moja ogólna zasada brzmi: jeśli można coś zrobić na linii montażowej, to prawdopodobnie warto to robić na linii montażowej.
Jednak linie montażowe nie zawsze cieszą się sympatią pracowników. Co kilka lat w mediach pojawia się informacja o kolejnej — zazwyczaj europejskiej — firmie motoryzacyjnej, która postanowiła odejść od linii montażowych na rzecz pracy grupowej, montażu pudełkowego, stacji montażowych i tym podobnych rozwiązań. Jak dotąd wszystkie te inicjatywy upadły, ponieważ linia montażowa pozostaje najlepszym rozwiązaniem! Przyjrzyjmy się długiej liście firm motoryzacyjnych, które próbowały i nie odniosły sukcesu w rozmontowywaniu linii montażowych. Linia montażowa wciąż jest królem produkcji!
Zanim pojawiły się linie montażowe
Linie montażowe Autocar Company, lata 1901–1912
Zanim wprowadzono linie montażowe, samochody były produkowane metodą budowy nadwozi („coach-building”). Proces ten wymagał wysoko wykwalifikowanych rzemieślników, którzy ręcznie budowali każdy samochód, jeden po drugim. Był to proces powolny, pracochłonny i kosztowny, przez co samochody były luksusem dostępnym jedynie dla najzamożniejszych.
Montaż w firmie Chalmers-Detroit Motor Company w 1910 roku
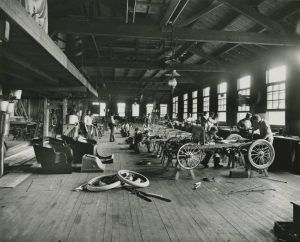
Produkcja odbywała się w tzw. halach montażowych, gdzie samochód składano w jednym miejscu. Wszystkie materiały, narzędzia i pracownicy gromadzili się przy tym stanowisku, aby zmontować pojazd. Było to najprostsze w organizacji, ponieważ kierownictwo nie musiało koordynować prac między różnymi stacjami. Jednak zarządzanie tym procesem na hali było znacznie trudniejsze. Wiecznie brakowało materiałów, dostarczano je z opóźnieniem albo zbyt wcześnie. Koordynacja między pracownikami również często szwankowała, przez co trudno było śledzić, co zostało już zrobione, a co jeszcze wymagało pracy. Szczególnie w sytuacjach, gdy pracownicy wykonywali jedynie konkretne zadania, dochodziło do nieporozumień. Na przykład montaż drzwi przed instalacją foteli czy deski rozdzielczej znacząco utrudniał dalsze prace.
Powstanie linii montażowych
Pakowanie mięsa w Chicago
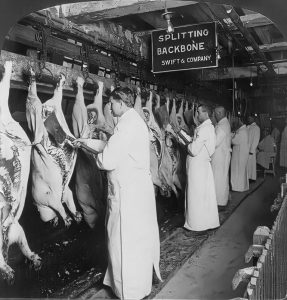
Koncepcja linii montażowej ewoluowała przez lata. Niektórzy uważają Arsenał Wenecki za przykład wczesnej linii montażowej. Linie montażowe były już stosowane do wypieku sucharów dla brytyjskiej marynarki w Plymouth w 1833 roku. W rzeźniach w Chicago około 1837 roku powstały tzw. „linie rozbioru” do przetwarzania świń. James Bonsack wynalazł maszynę do zwijania papierosów w 1881 roku, co ostatecznie przekształciło się w pełnowartościową linię montażową. W tym samym czasie pojawiły się linie montażowe do produkcji zapałek i puszek.
Linia montażowa magnesów Forda
W motoryzacji za prekursora linii montażowych często uważa się Oldsmobile, ale z powodu braku wymiennych części, pierwszą prawdziwą linię montażową w tej branży można przypisać Henry’emu Fordowi w 1913 roku. Obecnie linie montażowe są standardem w produkcji masowej ze względu na swoją wydajność, szybkość, możliwość planowania i niskie koszty. Te zalety znacząco przewyższają dodatkowy wysiłek związany z ich organizacją i wdrożeniem.
Krytyka linii montażowych
Linie montażowe często krytykowane są za odczłowieczanie pracy. Powtarzalność zadań, rygorystyczne ograniczenia czasowe i brak autonomii mogą prowadzić do utraty indywidualizmu i poczucia odłączenia od końcowego produktu. Pracownicy mogą czuć się jak trybiki w maszynie, a nie jak cenieni uczestnicy procesu produkcyjnego.
Krytyka ta jest szczególnie powszechna w Europie, zwłaszcza w Niemczech, gdzie miejsce pracy często postrzega się jako instytucję społeczną. W przeciwieństwie do tego w Stanach Zjednoczonych bardziej powszechny jest model „zatrudniaj i zwalniaj”, co prowadzi do odmiennego postrzegania roli pracownika w procesie produkcji.
Eksperymenty z odchodzeniem od linii montażowych
Volkswagen Salzgitter 1975
W 1975 roku Volkswagen w Salzgitter przeprowadził eksperyment z grupowym montażem silników przez dwudziestu ośmiu pracowników podzielonych na cztery zespoły. Zespoły te były odpowiedzialne za transport materiałów, testy i naprawy, a wewnętrzny podział zadań ustalano w grupach. Podczas gdy typowy montaż silnika miał cykl pracy trwający minutę, w tej stacji cykl wynosił aż czterdzieści pięć minut.
Eksperyment jednak się nie powiódł. Grupy reprezentujące pracowników czuły się zagrożone, ponieważ zespoły pracownicze negocjowały bezpośrednio z kierownictwem. Brakowało twardych danych dotyczących wydajności, a kierownictwo uznało tę metodę za nieodpowiednią do masowej produkcji. Eksperyment zakończono w 1977 roku po dwóch latach.
Volvo Kalmar 1984
W 1984 roku Volvo przeprowadziło eksperyment w Kalmarze w Szwecji, eliminując linie montażowe. Zamiast tego samochód był montowany w jednym miejscu przez grupę około dziesięciu pracowników. W praktyce był to powrót do metod stosowanych przed linią montażową Forda. Metodę tę nazwano „Volvoizmem” i wprowadzono ją ze względu na problemy z rekrutacją nowych pracowników oraz wysoką rotację.
Eksperyment nie odniósł sukcesu. Chociaż satysfakcja pracowników była nieco wyższa niż na tradycyjnych liniach montażowych, wydajność nie wzrosła. Problemy z logistyką materiałów i części komplikowały proces, a jakość nie uległa poprawie. Nawet poziom stresu pracowników pozostał na podobnym poziomie. W 1987 roku Volvo zdecydowało się przywrócić w Kalmarze konwencjonalne linie montażowe. Eksperyment trwał trzy lata, a fabryka została zamknięta w 2013 roku.
Opel Bochum około 1988 roku
W 1988 roku Opel Bochum (zakład uruchomiony w 1963 roku) przeprowadził eksperymenty z grupowym montażem, obejmujące składanie kokpitów w zespołach z cyklami pracy trwającymi od piętnastu do czterdziestu pięciu minut. AGV (Automated Guided Vehicle) transportował kokpit do następnej stacji. Publikacja z 1991 roku twierdziła, że planowano szerokie wdrożenie tej metody w całej firmie. Jednak nie ma wielu dostępnych informacji na ten temat, a nie wiadomo, czy wdrożenie kiedykolwiek miało miejsce. Osobiście wątpię, sądząc, że stosują linie montażowe jak wszyscy inni. Zakład został zamknięty w 2014 roku.
Jak się okazuje, lista zakładów motoryzacyjnych, które eksperymentowały z odchodzeniem od linii montażowych, jest tak długa, że potrzeba kolejnego wpisu na blogu. W następnej części opiszę trzy kolejne (również nieudane) eksperymenty. A teraz idźcie i NIE demontujcie swojej linii montażowej! Organizujcie przemysł!
Oryginalny wpis w języku angielskim i źródła zdjęć dostępne są na blogu autora: A Frequent Mistake—Undoing an Assembly Line—Part 1