Kanban, podobnie do systemów typu pull, takich jak CONWIP lub POLCA, stanowi podstawę zarządzania częściami w optymalnej produkcji. Wszystkie maksymalnie ograniczają liczbę elementów w procesie, poprzez dołączenie do nich pewnego rodzaju tokena (w tym wypadku karty kanban), który wraca na początek, gdy dana część opuszcza system.
Karty kanban funkcjonują zarówno jako karty fizyczne lub jako kanban elektroniczny. W tym tekście pokażę, kiedy używać fizycznej karty kanban, a kiedy jej cyfrowego odpowiednika.
Wprowadzenie
Karta kanban lub karta CONWIP, wielokrotnie okrążają pętlę procesu. Informacje zawarte na karcie (cyfrowej lub fizycznej) sygnalizują rozpoczęcie produkcji. Następnie, informacje poruszają się wraz z daną częścią poprzez cały proces produkcji, dobierając przy tym potrzebne zapasy. Gdy element opuszcza pętlę procesu, konkretna informacja wraca na początek i cały proces rozpoczyna się od nowa.
Szybkość karty
W dolnym odcinku strumienia procesu, do każdego elementu dołącza się informację, która porusza się z daną częścią. W związku z tym, w tym miejscu informacja nie może być szybsza niż element, z którym są powiązane. Niezależnie od tego, czy jest to informacja fizyczna, czy cyfrowa, prędkość jest taka sama jak prędkość części z nią powiązanej w danym procesie produkcji.
Jednak na powrocie (w górze strumienia), karta wraca na początek i ważne jest, by ta informacja czy to fizyczna czy cyfrowa, dotarła tam jak najszybciej. Im szybszy jest ruch informacji, tym krótszy czas uzupełniania i szybszy czas realizacji. Po powrocie informacji do kolejki produkcyjnej informacja musi czekać, a prędkość jej obiegu nie jest już tak ważna.
Faktem jest, że informacje cyfrowe mogą poruszać się znacznie szybciej niż informacje fizyczne, ponieważ uzupełnienie ich w systemie kanbana elektronicznego spowoduje ich gotowość do natychmiastowego odczytu. Niezależnie od tego czy system jest fizyczny czy cyfrowy, informacja jest uruchamiana przesunięciem części.
Fizyczna karta musi zostać przetransportowana z powrotem do miejsca pierwotnego przez jakąś osobę. Zazwyczaj karty są zbierane w skrzynce pocztowej i transportowane z powrotem do pierwszej maszyny w regularnych odstępach czasu.
W przypadku systemów cyfrowych wymagałoby to dodatkowej pracy np. skanowania (kod kreskowy, chipy RFID lub podobne) lub pisania. Taka sytuacja ma miejsce, na przykład w wypadku, gdy jakiś element zostanie dobrany z zapasów, lub wkrótce po przemieszczeniu ze stanowiska partii części. Gdy dane powrócą do cyberprzestrzeni, prędkość może być (prawie) równa prędkości światła. Na drugim końcu procesu, może pojawić się na monitorze lub jako wydruk, który musiałby być ponownie przetransportowany.
W zależności od sposobu zarządzania gromadzeniem i rozpowszechnianiem informacji cyfrowych, mogą one być wolniejsze niż informacje fizyczne. Na krótkich dystansach może nie być wcale różnicy między przekazaniem informacji w postaci elektronicznej czy fizycznej karty. Praca z kartą fizyczną może zająć jedną lub dwie godziny, a informacja cyfrowa może również zająć nam podobną ilość czasu – od trzydziestu minut do dwóch godzin (w zależności od konfiguracji). Nie stanowi to istotnej różnicy w procesie uzupełniania zapasów, który często jest mierzony w dniach.
Zdecydowanie inaczej wygląda to jednak przy dłuższych dystansach. Tutaj elektroniczna transmisja danych znacznie przewyższa transmisję danych fizycznych. Zakładając, że odbierasz swoje towary w Ameryce statkiem od dostawcy z Chin, czy wyślesz informacje dotyczące ponownego zamówienia pocztą? Statkiem trwałoby to nawet kilka tygodni, drogą powietrzną dni. A transmisja cyfrowa byłaby niemal natychmiastowa, choć jej obsługa może zająć kilka minut lub godzin.
Stąd warto wykorzystywać kanbana elektronicznego przy dłuższych dystansach. Nie musimy tu mówić tylko o takich odległościach jak Ameryka i Chiny, bo nawet jeśli twój dostawca jest w innym mieście, korzystniejsza może być transmisja cyfrowa. Ale zanim podejmiesz decyzję w oparciu o szybkość przepływu informacji, należy pamiętać, że jest więcej rzeczy do wzięcia pod uwagę w całym procesie.
Zrozumienie sytuacji
Innym ważnym czynnikiem jest zdolność zrozumienia obecnej sytuacji w procesie. Jak wyglądają konkretne prace oraz przypisane do nich karty? W tym miejscu ważne jest rozróżnienie spojrzenia na funkcjonowanie systemu – z perspektywy menedżera siedzącego za biurkiem oraz operatora na hali produkcyjnej.
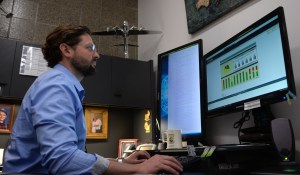
Menedżer lubi kliknąć na swoim komputerze i zobaczyć aktualną sytuację w swoim systemie ERP. Działa to
w dowolnym miejscu na świecie, o ile ma połączenie z bazą danych. Często jest to nawet preferowany sposób, w jaki menedżer ma dostęp do danych, a wielu menedżerów spędza mało czasu w hali produkcyjnej.
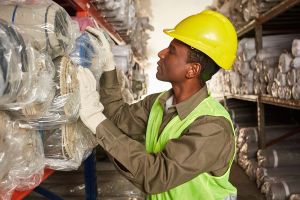
Pracownik, z drugiej strony, chce zobaczyć sytuację na hali produkcyjnej, która nie wymaga od niego zalogowania się do systemu, z którym może lub nie może być zaznajomiony, lub do którego może nawet nie mieć praw dostępu. Dlatego woli fizyczną wersję informacji.
Menedżerowie czasami mają tendencję do postrzegania siebie jako ważniejszych od pracowników i myślą, że jeśli jest coś dla nich dobre, będzie to dobre dla wszystkich innych. Niestety, niekoniecznie jest to prawda. Zwłaszcza w przypadku danych dotyczących hali produkcyjnej, gdzie ludzie tam pracujący mają o wiele częstszą i znacznie pilniejszą potrzebę zrozumienia bieżącej sytuacji niż menedżer, wymagający łatwej dostępności do danych, których czasem nawet wcale nie przegląda. Wiąże się to bardzo ściśle z zarządzaniem wizualnym.
Podsumowując, fizyczna prezentacja danych jest często znacznie korzystniejsza dla hali produkcyjnej, gdzie pracownicy często muszą znać nadchodzące zamówienia, aby dostarczyć materiały i zaplanować obsadę maszyn.
Z drugiej strony, jeśli nie ma hali produkcyjnej, a tylko logistyka, jest to mniej istotne. Kierowca ciężarówki nie otworzy swojej ciężarówki, aby sprawdzić, co jest załadowane, ale raczej woli odnieść się do dokumentów załadunku. Stąd, jeśli nie znajdujesz się w hali produkcyjnej, to fizyczne dane są z reguły znacznie mniej potrzebne.
Ciągłe doskonalenie
Lean „żyje i oddycha” ciągłym doskonaleniem. Jeśli chodzi o informacje cyfrowe i fizyczne, zdolność do ciągłego doskonalenia jest o wiele łatwiejsza w systemach fizycznych. Zmiana obsługi informacji (karty kanban) jest znacznie łatwiejsza, jeśli jest to kartka papieru niż w przypadku kanbana elektronicznego. Sprawdzenie obciążenia pracą i poziomów zapasów w celu dostosowania obsady lub liczby kart jest również znacznie łatwiejsze w systemach fizycznych.
Oczywiście można to również zrobić w systemach cyfrowych. Potrzebny jest jednak dodatkowy programista lub specjalista ds. używanego systemu. Jeśli już takiego będziemy mieć, należy mu przekazać co jest potrzebne i w jaki sposób ma działać, a następnie mieć nadzieję, że wykona to tak, jak tego tak naprawdę chcesz. Zwykle proces optymalizacji wyhamowuje, jeśli wszystko jest przenoszone do systemów komputerowych.
A co, jeśli… obie?
Być może myślisz: jeśli zarówno systemy fizyczne, jak i cyfrowe mają zalety, czy mogę wykorzystać oba systemy i uzyskać zalety obu? Nie!
Naprawdę, nie rób tego! Rzecz jasna, będziesz miał dwa razy więcej pracy, tworząc dwa systemy. Ale znacznie większym problemem jest to, że te dwa systemy będą się różnić. System cyfrowy mówi A, a system fizyczny mówi B. Co zrobisz, jeśli operator w hali produkcyjnej musi uzyskać jeden jasny sygnał, a nie dwa sprzeczne komunikaty. Podczas, gdy wszystko działa w teorii, w praktyce może być znacznie większy chaos. Dlatego nie należy mieszać obu systemów.
Dobrym pomysłem wydaje się drukowanie papierowych kart z systemu cyfrowego. Możliwe jest również, skanowanie kart w celu zaktualizowania systemu fizycznego. Ale tylko jeden z nich może być najważniejszy.
W związku z czym, albo karty są tylko kopią cyfrowego świata, albo cyfrowy świat to tylko licznik fizycznych kart. Jeśli istnieją różnice między systemami, jeden z nich musi ustąpić miejsca drugiemu… choć informacja fizyczna zazwyczaj jest bardziej poprawna.
Podsumowanie
Więc co powinieneś zrobić? To, co ja zalecam, to wykorzystanie informacji cyfrowych przy większych odległościach (w różnych zakładach). Zapewni to szybszy czas uzupełniania, a ponieważ prawdopodobnie nie jest to linia produkcyjna, ale proces logistyczny, zarządzanie wizualne nie jest tak istotne. Jeśli twój przepływ informacji odbywa się w obrębie zakładu, informacje fizyczne mogą być znacznie łatwiejsze do zrozumienia. A teraz idź, łap płynące na hali informacje i działaj!
Oryginalny wpis w języku angielskim dostępny jest na blogu autora:
Should You Use Physical or Digital Kanban Cards?