Wielkim krokiem w kierunku perfekcji w szczupłym systemie produkcyjnym jest dojście do przepływu jednej sztuki. Jednak niewiele osób zdaje sobie sprawę, jaki ogromny wysiłek i dyscyplinę utrzymuje Toyota w celu osiągnięcia tego celu. Podczas mojej wizyty w fabryce Toyoty i konferencji APMS w Tokio w 2015 r. widziałem kilka wspaniałych przykładów o tym świadczących. Spójrzcie na to…
Wprowadzenie
Podczas gdy w tradycyjnym rozliczaniu kosztów mniejsze rozmiary partii zwykle oznaczają wyższe koszty lub nakłady na przezbrojenia, Toyota już dawno zdała sobie sprawę, że koszt ten jest więcej niż rekompensowany uzyskiwaną elastycznością i zmniejszeniem zapasów. Przy mniejszych rozmiarach partii potrzebujesz mniej zapasów, dzięki czemu możesz szybciej reagować na zmiany w systemie produkcyjnym. Podczas, gdy świat zachodni często dąży również do mniejszych rozmiarów partii, wydaje się, że istnieje wiele przypadków, w których dalsze zmniejszenie wielkości partii jest uważane za zbyt drogie. Jednak nie dla Toyoty i Denso.
Zautomatyzowane wózki (AGV vs AGC)

Podczas mojej wizyty w Japonii w fabryce Toyoty w 2015 r. Zauważyłem coś ciekawego. Jestem pewien, że wszyscy wiecie o automatycznych pojazdach kierowanych (AGV), pojazdach sterowanych komputerowo do transportu materiałów. Zwykle mają określony rozmiar, a następnie starasz się na nim przewieźć jak najwięcej materiału.
Jednak w Toyocie zauważyłem dziwnie mały wózek AGV. Był znacznie mniejszy niż normalny AGV – odpowiadał rozmiarowi dużej walizki. Ten AGV przewoził dokładnie jeden przedni i jeden tylny zderzak.
Później dowiedziałem się, że Toyota nazywa te pojazdy automatycznie kierowanymi wózkami (AGC), a nie automatycznie kierowanymi pojazdami (AGV). Widziałem także filmy z różnych wózków dla innych części używanych w innych lokalizacjach w grupie Toyoty, a mianowicie w Denso.
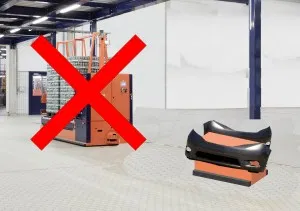
Ponieważ nie pozwolono mi robić zdjęć w Toyocie, zdjęcie tutaj to fotograficzna wersja innej hali produkcyjnej, aby dać ci poczucie wielkości AGC.
Dantotsu
Poniższe przykłady pochodzą z prezentacji na APMS 2015 Katsuhiko Sugito, dyrektor Centrum Innowacji Produkcji w Denso. Denso jest częścią grupy Toyota i moim zdaniem wdrożył system produkcyjny Toyoty nawet lepiej niż Toyota.
Denso dąży do tego, co nazywają Dantotsu . To połączone słowo Danzena (断然 oznacza zdecydowanie, absolutnie, zdecydowanie, wyjątkowo) i angielskie słowo Top . Ich celem jest bycie absolutnie najlepszym; nie zaakceptują drugiego miejsca. (Należy pamiętać, że Dantotsu jest słowem wewnętrznym Denso, a nie [jeszcze] częścią zachodniego chudego słownictwa.)
Jednym z tych celów jest wszędzie prawdziwy przepływ jednej sztuki. Ilekroć potrzebne są części, jest jedna maszyna, która składa dokładnie jedną część, gdy ta część jest potrzebna. Brzmi prosto? Następnie zastosuj to do odlewów aluminiowych!
Odlewanie po jednej sztuce
Zwykle odlewanie jest operacją wsadową. Duża ilość wlewków aluminiowych jest topiona, odlewana jest większa liczba części, a następnie cała partia jest umieszczana w piecu do obróbki cieplnej. Zmniejszenie tej operacji do wielu rozmiarów i podłączenie jej bezpośrednio do linii montażowej brzmi szalenie. Dlatego byłem bardzo zaskoczony i zdziwiony, gdy dowiedziałem się, że w Denso to zrobiono!
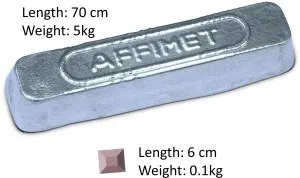
Denso radykalnie zredukowało wszystkie etapy produkcji do rozmiaru jednej sztuki. Do topienia aluminium nie mogli użyć standardowych prętów przemysłowych, które zwykle ważą około 5 kg i mają około 70 cm długości. Do swoich produktów potrzebowali znacznie mniejszych wlewków.
To był spory wysiłek, ale w końcu znaleźli dostawcę, który dostarczył im mini-wlewki w kształcie piramidy o wadze zaledwie 100 gramów i długości około 6 cm.
Obraz tutaj jest tylko dla zilustrowania różnicy wielkości sztabek. Pokazany duży wlewek jest obrazem standardowego wlewka 5kg, a mniejszy (brązowy) jest moim szkicem pokazującym różnicę, ponieważ pan Sugito poprosił nas, abyśmy nie publikowali jego zdjęć.
W rezultacie potrzebowano tylko jednej, znacznie mniejszej maszyny do stopienia aluminium, co zmniejszyło zajmowaną objętość na hali (długość, szerokość i wysokość) ponad 300-krotnie. Co zaskakujące, mała maszyna okazała się również bardziej energooszczędna.
Zastosowano także znacznie mniejszą maszynę odlewniczą. Ojętość maszyny została zmniejszona do 1/5. Nowa elektryczna maszyna odlewnicza zużywa nie tylko znacznie mniej energii niż poprzednia maszyna hydrauliczna, ale również uzyskiwana jakość jest znacznie lepsza.
Wreszcie, piec do obróbki cieplnej również został zmieniony z dużego pieca okresowego na mniejszy zsyp grawitacyjny (karakuri). Ponieważ części wchodzące do pieca są w tym przypadku wciąż gorące, proces stał się szybszy i zużywa mniej energii. Rozmiar pieca został również zmniejszony ponad 40-krotnie.
Ogólnie, nowy system był znacznie mniejszy niż stary i zużywał połowę energii, nie wspominając już o lepszej jakości, mniejszych zapasach, większej elastyczności i krótszym czasie realizacji.
Kucie po jednej sztuce
Podobnie jak w przypadku odlewu, zmniejszono rozmiar maszyny kuźniczej. Dużą prasę ogólnego zastosowania zamieniono na znacznie mniejszą, która w razie potrzeby produkowała tylko jedną część.
Cięcie po jednej sztuce
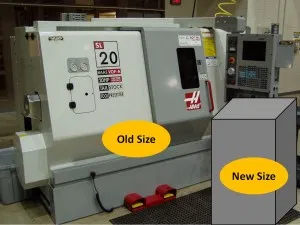
Jeszcze innym przykładem było narzędzie tnące. Zastąpili narzędzie CNC normalnej wielkości znacznie mniejszym narzędziem o wielkości 1/4 i o 1/3 tańszym.
Obraz tutaj jest moją własną ilustracją opartą na zdjęciach stockowych, a nie oryginalnych maszynach Denso.
W prezentacji było więcej przykładów podobnego zmniejszania wielkości maszyn w celu uzyskania przepływu jednej sztuki – takich jak tokarki, obróbka powierzchni i oraz przykłady łączenia maszyn. Dokonano również przeglądu przepływu materiału, przy czym AGC z góry jest tylko jednym z przedstawionych przykładów.
Koszt, koszt…
Najprawdopodobniej, jeśli przedstawisz którąkolwiek z powyższych sugestii dotyczących rachunku kosztów w swoim zakładzie, księgowemu prawdopodobnie wyjdą żyły na wierzch. Tradycyjna kalkulacja kosztów jest wysoce nieodpowiednia do usprawnień typu lean. Rozliczanie kosztów bardzo dobrze mierzy koszty, ale nie nadaje się do pomiaru korzyści. A jeśli księgowy nie będzie w stanie tego zmierzyć, wówczas ustawi korzyść na zero (i prawdopodobnie nawet w to uwierzy).
Jednak korzyść jest zdecydowanie widoczna. Denso zgłasza wiele korzyści przewyższających koszty, takie jak elastyczność, redukcja zapasów, mniejsze zużycie energii, większa dostępna powierzchnia podłogi, a tym samym mniejsza odległość transportu i wiele innych. Większość z nich jest trudna do oszacowania, ale Denso jest przekonane, że są na dobrej drodze, aby stać się najlepszym z najlepszych „Dantotsu”, i zgadzam się z tym.
Oczywiście niekoniecznie oznacza to, że od razu powinieneś dążyć do produkcji odlewów po jednej sztuce. Przepływ jednej sztuki w odlewaniu będzie dawał niewielką korzyść, jeśli reszta twojej firmy ma duży rozmiar (razy 500). Jak zawsze, zacznij od łatwych, nisko wiszących owoców. Jeśli jesteś typowym europejskim zakładem, prawdopodobnie masz kilka łatwiejszych sposobów do ulepszenia procesu, zanim wybierzesz tak radykalną zamianę maszyny odlewniczej.
Pomyśl o tym. Jaki projekt ulepszenia daje ci najlepszy zwrot z inwestycji w obecnej sytuacji? Masz jeden? A teraz wyjdź, rozpocznij najbardziej korzystną i pilną poprawę i usprawniaj swoją firmę!
Oryginalny wpis w języku angielskim dostępny jest na blogu autora:
Toyota’s and Denso’s Relentless Quest for Lot Size One
Ok. Przepływ jednej sztuki to potężne narzędzie, ale…
Mamy już rok 2020, sytuację z chińskim wirusem i biznes nie jest już taki jak 5 lat temu…
Właśnie TESLA zdetronizowała Toyotę z pozycji najbardziej wartościowej marki, a sama Toyota stoi przed nie lada wyzwaniem związanym z rosnącą lawinowo koniecznością automatyzacji procesów produkcji oraz wykorzystaniem sztucznej inteligencji w procesach zarządzania.
Chcesz poznać za pomocą jakich technik rozwiązywane są problemy w najnowocześniejszych i najbardziej rentownych firmach produkcyjnych na świecie?
Zapraszam do kontaktu.
Ad vocem Toyoty: kapitalizacja a wartość to jednak dwie różnice kwestie.