Plan-Do-Check-Act (lub PDCA) jest jednym z kluczowych elementów w lean manufacturing we wszystkich procesach usprawniających. Moim zdaniem, jest to podstawa jakichkolwiek zmian. Wszystkie inne narzędzia występują w oparciu właśnie o PDCA.
Wg mojego doświadczenia, większość porażek projektów lean realizowanych w zachodnim, wynika nie z powodu użytych narzędzi, ale dlatego, że zaniedbywane jest poruszanie się zgodnie z PDCA. Oczywiście (prawie) wszyscy wiedzą, czym jest PDCA, ale jest ogromna różnica między poznaniem teorii a prawidłowym jej wykorzystaniem. W tym wpisie wyjaśnię bardziej szczegółowo, jak należy działać PDCA. W następnych wpisach pokażę typowe pułapki PDCA, jego historię i wiele, wiele różnych wariantów PDCA, które tam są.
Co to jest PDCA?
Planuj (Plan)

Pierwszym krokiem w PDCA jest Plan. Jak sama nazwa wskazuje, planujesz, co zamierzasz zrobić. W zależności od projektu może to być największa część wysiłku PDCA. W rzeczywistości można go zobaczyć jako liczbę pod-kroków lub punktów, które należy umieścić w planie . Zależnie od postępu, być może będziesz musiał zrobić kilka z nich iteracyjnie, aż do uzyskania odpowiedniego rozwiązania.
- Zdefiniuj zakres: jakiego problemu szukasz?
- Zdefiniuj cel: co chcesz osiągnąć? Jakie są Twoje cele?
- Analizuj sytuację: spróbuj zrozumieć, jaka jest aktualna sytuacja. Rozmawiać z ludźmi. Odwiedź miejsce pracy i obserwuj (Genchi Genbutsu). Zbieraj dane.
- Opracuj rozwiązanie jak podejść do problemu aby znaleźć skuteczne rozwiązanie
- Wybierz najlepsze rozwiązanie: spośród różnych pomysłów na rozwiązania, wybierz ten, który wg Twojej opinii jest najbardziej obiecujący i daje największe szanse powodzenia.
Plan obejmuje wiele zagadnień. Osobiście, jeśli miałbym za zadanie zmodyfikować PDCA, włożyłbym jeszcze kilka innych liter poza samym Plan. Ale zaraz, zaraz… już znaleźli się tacy, którzy zmodyfikowali PDCA. Nie jestem jednak przekonany o wynikach poczynionych modyfikacji przez niektórych z nich (więcej szczegółów o odmianach PDCA wkrótce).
Wykonaj (Do)
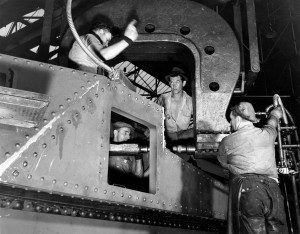
To jest rzeczywiste wdrożenie. Wprowadź zmianę, może to być miejsce pracy, produkt, spraw by ta zmiana się dokonała. Prawdopodobnie napotkasz problemy podczas tej fazy, o których wcześniej nie myślałeś. To jest normalne. Po prostu rozwiąż je, kiedy się pojawią.
W każdym razie spróbuj wykonać tą zmianę. Na przykład, jeśli zmienisz sposób pracy pracowników, łatwo jest sprawić by ten jeden raz zrobili to w ten sposób. Dużo trudniej jest zastosować się do zmiany na stałe. W zależności od problemu, który próbujesz rozwiązać, standaryzacja naprawdę może tu pomóc. Stwórz standard, przeszkól pracowników i potwierdź, że pracują według nowego standardu także kilka dni później.
Sprawdź (Check)
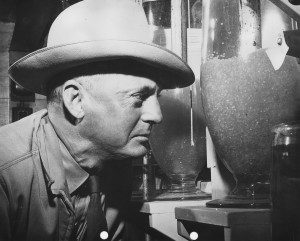
Jest to prawdopodobnie najczęściej pomijana część PDCA. Czy Twoje wdrożone rozwiązanie działa w rzeczywistości? Czy osiągane są zaplanowane cele? To bardzo poważne pytanie. Sądząc z mojego doświadczenia, w większości przypadków nie, lub przynajmniej nie na tyle ile była zaplanowane.
Zbyt często, kierownictwo jest zadowolone z sprytnie wyglądającej prezentacji i pomijane jest sprawdzenie tego co w rzeczywistości dzieje się na warsztacie. Dodatkowo, kierownictwo ignoruje również efekt Hawthorne’a. Efekt ten został po raz pierwszy zauważony w Hawthorne Works of Western Electric w 1930 roku i został nazwany w 1950 roku. W wielu przypadkach zmiana czegoś na hali produkcyjnej poprawi system niezależnie od tego, co zmienisz – ale tylko na krótki czas! Innymi słowy, uwaga kierownictwa podczas procesu zmiany w warsztacie doprowadzi do zwiększenia wydajności i lepszej jakości, niezależnie od tego, co zostanie faktycznie realizowane. Jednak, gdy tylko kierownictwo zakończy działania, wszystko wróci do starego stanu.
Jest to bardzo częsta pułapka. Robisz projekt, KPI poprawiają się, przechodzisz dalej, a KPI następnie odwraca się i spada. Aby poprawić projekt, poprawa nie tylko musi działać, ale również musi działać ciągle. To jest cała idea części Sprawdzenie w PDCA.
Działaj(Act)

Co robić dalej jest zależne od wyniku fazy Check . Jeśli Twoja implementacja nie osiągnęła celów, musisz dowiedzieć się, dlaczego. Dlaczego Twoje rozwiązanie nie działa zgodnie z oczekiwaniami? Prowadzi to do powtórzenia PDCA z innym Planem, aby ustalić nowe lub lepsze rozwiązanie w celu osiągnięcia Twoich celów.
Jeśli uda Ci się osiągnąć cele (bez powrotu po dwóch tygodniach, pamiętaj o tym!), Powinieneś pogratulować zespołowi i okazywać uznanie!
Jednak praca nigdy się nie kończy. Teraz musisz pomyśleć o tym, który problem będzie rozwiązany jako kolejny. Wybierz najodpowiedniejszy (najczęściej jeden z najlepiej oczekiwanymi korzyściami dla tego wysiłku) i rozpocznij nową PDCA.
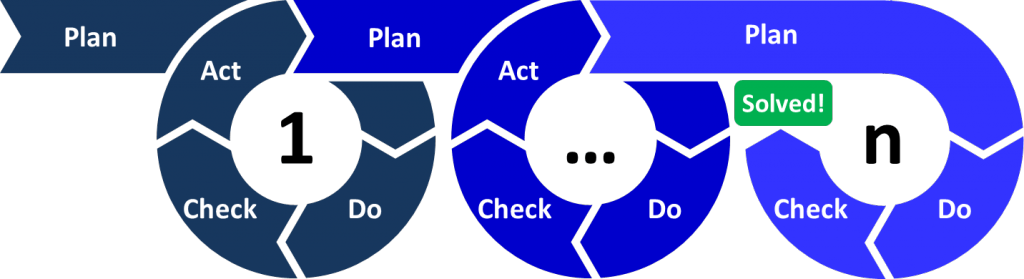
Podsumowanie
Ogólnie rzecz biorąc, PDCA jest dla mnie podstawowym podejściem pod wszystkimi działaniami doskonalącymi. Wiem, że to nie jest łatwe. Często spotykam się z pominięciem kroków lub wykonaniem PDCA bezskutecznie, jeśli nie poświęca mu się potrzebnej uwagi. Podczas gdy pierwsze dwa kroki, Plan i Do, przychodzą naturalnie dla większości menedżerów projektów, rzeczywiste i właściwe Check i Act jest znacznie rzadsze. Czasami mam nawet poczucie, że Check and Act nie są naprawdę potrzebne w przemyśle.
Mam nadzieję, że twój szef ma otwarty umysł na takie rzeczy i możesz nie tylko planować i robić, ale także sprawdzać i działać w celu dążenia do najlepszej organizacji!
Oryginalny wpis w języku angielskim dostępny jest na blogu autora:
The Key to Lean – Plan, Do, Check, Act!